Stainless steel spiral pipes are considered an essential part of the equipment for many industrial applications since they are strong, anti-corrosive, and pliable. In this article, the main areas of use and the beneficial features of stainless steel coiled pipes will be described, pointing out such branches as the extraction and processing of oil and gas and the production of medical appliances. It will be possible to define service properties that facilitate efficient exploitation of these pipes in negative temperatures, examine working dimensions specifications, and outline principles of design of installed parts responding to new challenges. Knowing the complex parameters and operating characteristics of stainless steel coiled pipes will help professionals to use and operate the coiled pipes most effectively.https://ssalloy-steel.com/stainless-steel-pipe/
What is Stainless Steel Tubing and How is it Made?
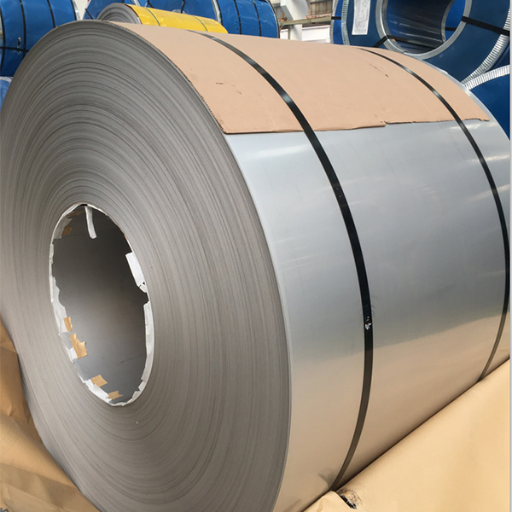
What is Stainless Steel Tubing and How is it Made
Stainless steel tubulars are strong, corrosion-resistant, alloyed tubes that can transfer liquid and gases in the medical and industrial fields. The production of the tubing begins with picking the raw material, usually made up of billets or coils of stainless steel. These materials are thoroughly cleaned, heated, and formed into the desired tube shape by extrusion or welding. Conveying the material through an extruder allows it to achieve the required diameter by forcing it through a die while making welded tubing, which involves shaping flat steel strips into a cylinder and welding its edges. The subsequent stages involve tube heat treatment and polishing to improve the tubes’ surface finish and mechanical properties. Testing and evaluation are key quality control components to guarantee that tubulars have specified dimensions and tolerances free of defects and ensure operational efficiency in various industrial applications.
Understanding the Stainless Steel Composition
To better appreciate the manufacture of stainless steel, I shall need to study its components, including iron, chromium, nickel, and carbon. Of these, chromium is perhaps the most important since it is common for chromium content to be at least 10.5% of the alloy and is responsible for forming a passive film of chromium oxide on the surface, which helps prevent corrosion. Nickel helps in toughness and flexibility, while carbon assists in hardening and strength factors. No al lack of molybdenum to mention, these and other elements enhances corrosion resistance properties of steel in very harsh environments. From my understanding, the stainless steel grades are many, e.g., 304 and 316, and their composition differs depending on the intended service and environmental conditions. These elemental variations are essential in determining the appropriate stainless steel type for specific industrial applications.
Manufacturing Process of Seamless Tubing
Seamless stainless steel tubing manufacturing is a complex operation with several processes geared toward the products’ constancy, strength, and accuracy. To begin with, a furnace is used to heat the raw material billets to between 1200 degrees Celsius and 1250 degrees Celsius. The volume of raw material billets is considerable; therefore, it is critical to establish a rotary piercing essential function before mass-deforming the blanks. These blanks are compressed into a hollow end through a bar piercing mill at this stage. Further along during this stage, the apparent beginning tube continues to be stretched by a stretch-reducing mill that decreases the diameter and wall thickness while still guaranteeing uniform standards.
Some technical parameters at this stage of processing include the need for excessive control over the external diameter of the tube, which falls within the range of 4m m to 219mm, and the thickness of the tube wall, ranging from 0.5mm to 20mm. Such dimensions enable the producers of seamless iron pipes and tubes to conform to industry standards. Following deformation and forming, heat treatment, for example, an annealing process, is performed to minimize internal stresses and improve flexibility and the ability to withstand corrosion. A range of advanced non-destructive testing methods, including ultrasonic testing, are used to check the structural integrity of the tube if there are any internal inconsistencies so that it has a high standard. Due to the thorough manufacturing process of the tubing, the seamless tubing is suitable for a wide range of industrial uses.
Key Differences: Welded vs. Seamless Tubing
Several critical differences arise from their manufacturing processes, structural integrity, and applicable uses when comparing welded and seamless stainless steel tubing, which ultimately influence their suitability for specific industrial applications.
Manufacturing Process: Welded tubing is made by curling a flat steel strip into a tube shape and sealing the joint with a longitudinal weld seam. This process offers efficiency and cost-effectiveness, rendering welded tubes more economical for longer lengths. Conversely, seamless tubes are produced from solid billets pulled over a piercing rod to create a hollow tube without weld seams, ensuring uniformity and strength.
Structural Integrity: The absence of a weld seam in seamless tubing improves pressure resistance and enhances structural robustness, making it ideal for high-pressure environments. Welded tubing, while possessing a slightly reduced pressure tolerance due to the seam, generally meets strength requirements for a broad range of less demanding applications.
Technical Parameters: Seamless tubing typically exhibits higher tensile properties due to the lack of weld seam. The dimensional accuracy and wall thickness of seamless tubes are more variable than welded tubes, which can be manufactured with tighter tolerances. Typical sizes for seamless tubing range from 4mm to 219mm in outer diameter and 0.5mm to 20mm in wall thickness, while welded tubing can be produced in larger diameters with similar thickness.
Application Suitability: Choose between welded and seamless tubing hinges based on specific project needs. Seamless tubing’s uniform structure best suits critical applications like the oil and gas industry or chemical processing, where reliability against bursting and cracking is paramount. Welded tubing is prevalent in plumbing, heat exchangers, and decorative architecture due to its cost benefits and adequate performance characteristics.
By understanding these differences, professionals can make informed selections to ensure operational efficacy and economic viability in their respective domains.
What are the Benefits of Using Stainless Steel Coiled Tubing?
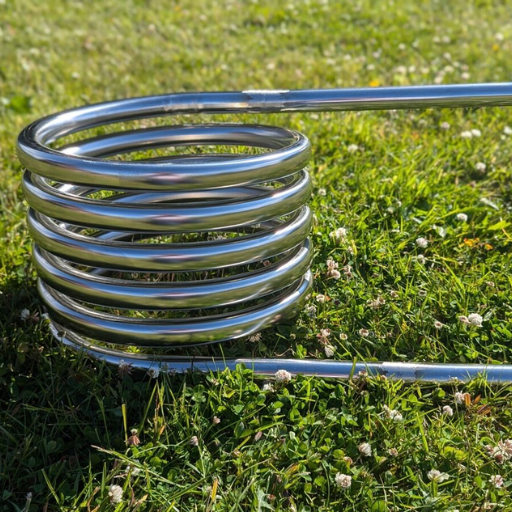
What are the Benefits of Using Stainless Steel Coiled Tubing
Stainless steel coiled tubing is an advantageous option mainly because it is mechanically robust and has corrosion resistance. To begin with, coiled tubing is supplied in a continuous form, enabling long runs without any joints, reducing potential leak points, and enhancing the system’s integrity. This is important in applications involving high pressures, such as in the oil and gas industry. Furthermore, stainless steel strength and toughness leave tubes capable of withstanding extremes at high temperatures and graphite environments, thus extending service life and reducing maintenance intervals and costs. In addition, the coiled tubing property that makes it flexible makes it easier to install in awkward shapes, thereby increasing the efficiency of operations while driving down the cost of labor. These factors contribute to the dependable efficiency and economic viability of stainless steel coiled tubing in different industries.https://ssalloy-steel.com/blog/stainless-steel-pipe/
Advantages of Corrosion Resistance
Based on what I have seen, the benefits of stainless steel, especially in industrial use, concerning corrosion resistance appear pretty compelling. First and foremost, corrosion resistance makes it possible for the components to be exposed to severe conditions of use for a more extended period without undue wear. This resilience naturally results in a decline in the number of times these components need to be maintained or changed, in addition to the costs involved. Moreover, corrosion-resistant materials also help preserve the soundness of the structure itself and thus help avoid contamination in food and pharmaceutical areas where cleanliness is crucial. There is also greater assurance of safety due to smaller chances of failure of systems caused by the degradation of materials, which are very important in the oil and gas sectors, for example, where system integrity is critical. Given this, the use of corrosion-resistant stainless steel means significant savings in the long run in terms of the reliability of the systems in question.
Importance of Wall Thickness and Outer Diameter
In my experience, the wall thickness and outside diameter should be emphasized in terms of their significance as tubular construction requirements for stainless steel tubing. This is because the wall of the vessel influences the strength –weight – and pressure rating of the tube, with thicker walls having increased durability, pressure rating, and resistance, which in turn are best suited for high-stress applications. The converse is true for thin-walled tubular sections where light constructions are required, and weight is essential. However, the outer diameter determines the flow rate and the system’s compatibility with existing systems. The ability to correctly size both parameters guarantees that the tube will perform optimally while ensuring safety. It is common practice to notice the outer diameter range between 4mm and 219 mm. In contrast, the wall thickness range between 0.5 and 20 mm is familiar with the industry’s most seamless and welded tubing. Such dimensions are necessary to meet the project’s needs so that the system installed is functional and has a long life.
Why Choose 316 Stainless Steel for Industrial Applications?
316 stainless steel is the most viable product subjected to corrosion because of its manufacturing process and suitability for the operating environment. Due to its chemical design comprising molybdenum, 316 stainless steel is also resistant to other corrosive elements such as acidic compounds and chlorides. Additionally, the tensile strength is within the range of 515 MPa to 730 MPa, which is augmented by the elongation at a break of 40%, thereby promoting the steel during application. The metal is also straightforward, especially for welding and forming. Hence, it is used broadly in many designs, architecture, and industrial constructs. Conversely, 316 stainless steel is designed to maintain strength over wide temperature ranges from cryogenic to moderately high temperatures. Industrialization of these qualities ensures a longer life span and precision in cases where failure of an application is not permissible.
How to Choose the Right Stainless Steel Tubing Coil for Your Needs?
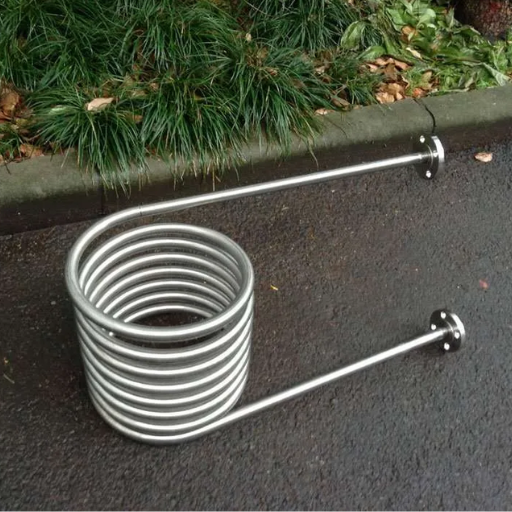
How to Choose the Right Stainless Steel Tubing Coil for Your Needs
Various important factors must be addressed when choosing the suitable stainless steel tubing coil to ensure it works well and is economical. Start with the application needs, such as the fluid or gas that will be carried in the tubing, the pressure and temperature that will be applied, and the environmental conditions the tubing will face. The grade of stainless steel should be such that it is capable of handling the corrosive nature of the environment and possessing the required strength; 316 stainless steel is commonly preferred in many industrial applications because of its better grade, especially in chloride and acidic environments. These variables also are the tubing’s wall thickness and outer diameter, as these parameters determine the tubing’s pressure rating and flow rate, respectively. Installation conditions also need to be looked at since coiled tubing will provide a much easier way to integrate into more complicated layouts. Also, consider any regulations or standards applicable in the industry that may require specific stainless steel tubing specifications for the application or testing standards. In this way, the engineers do not take any chances as they determine the specifications of the tubing coil with which they will carry out their operations and withstand the environment in which they operate.
Factors to Consider: Length and Diameter
When selecting stainless steel tubing, both length and diameter are critical aspects that should align with specific operational requirements and industry standards. The length of tubing directly affects installation and integration into existing systems. Standard coiled lengths typically range from 1,000 feet to over 10,000 feet, depending on application needs, allowing for fewer connections and reduced potential for leakage. The correct length facilitates efficient flow and minimizes wastage.
Similarly, the diameter of the tubing is pivotal as it determines the flow capacity and pressure requirements. Typical outer diameters range from 1/16 inch to 2 inches, depending on the fluid volume being transported and the system’s pressure specifications. For example, a smaller diameter is apt for precise flow control in applications like instrumentation, whereas larger diameters are suited for high-capacity distribution systems. Both parameters should be evaluated by ANSI/ASME B36.19 and ASTM A269 standards to ensure compliance and performance reliability. In conclusion, carefully considering length and diameter helps ensure operational efficiency and system safety, supporting an optimally functioning installation.
Evaluating Pipe and Fitting Requirements
While evaluating pipe and fitting requirements, I always focus on several aspects to achieve a robust and reliable system. First of all, it is essential to identify the needs of the application, such as what is being transported, the pressure, and the temperature. I am also concerned about the corrosion resistance of the materials, and I often prefer the stainless steel type 316 because of its superior corrosion resistance. In addition to these, I also have size and capacity requirements so that the pipes selected with their geographical dimensions – the diameter and thickness of the walls – meet the operational requirements and standards rules such as ANSI and ASTM. It is also necessary to fulfill the suaqualificationalla requirements that the fitting must made of the same material as the piping and be capable of withstanding the same operational stresses. Finally, the choice between flexible and rigid solutions is influenced by installation considerations like the degree of complication and exposure to the external environment. Following these steps systematically enables me to select pipes and fittings that work efficiently for a long time.
The Role of Corrosive Environments in Material Selection
The basic problem in selecting materials for corrosive environments is determining their resistance against the specific aggressors. For example, in sodium chloride or sulfuric acid environments, the preferred material is usually 316 stainless steel, which offers maximum protection against pitting and crevice corrosion. Such corrosion environments require materials capable of resisting chemical attacks together with physical and mechanical stresses over time. In the case of the enumeration of some technical parameters, the pH value of the substance (from 0 to 14) is included, which is significant in determining the material. These values are also helpful in assessing temperature, which increases the oxidation of metallic substances. The usual range would be from absolute zero (-238°F) to moderately high (800°F). Finally, these include the assessment of tensile strength, which would average from 515 MPa to 730 MPa for stainless steel, and compliance with relevant industry standards such as NSF or ISO. These approaches guarantee that the material selected would withstand the design and the reliability and performance requirements of very harsh environments.
What are the Typical Applications of Stainless Steel Coiled Pipe?
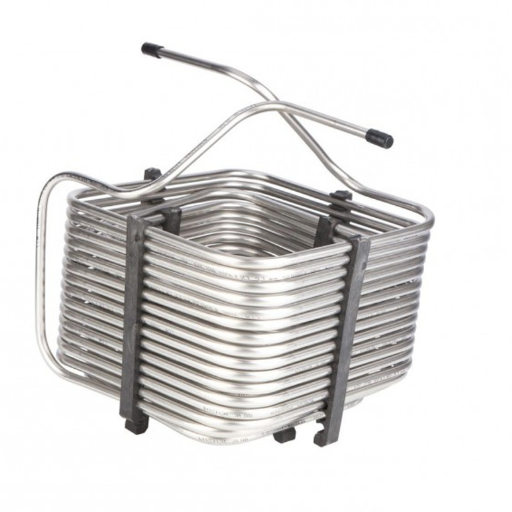
What are the Typical Applications of Stainless Steel Coiled Pipe
Applying stainless steel coiled pipes is becoming widespread in many industries owing to its strength, flexibility, and anti-corrosive properties. In the oil and gas market, they are extensively applied for healthy intervention and drilling; therefore, hydraulic means are also provided because of their continuous structure, which reduces the number of leak points and can endure high-pressure levels. Coiled pipes are also used in the chemical and petrochemical industry to transport harsh chemicals because of their rust-resistant characteristics. Also, the fans ‘ temperature tolerance property allows them to be used as a component in heat exchangers. Additionally, the pharmaceutical and food industries have adopted these materials because of their high sanitary standards and ease of sterilization, ensuring the products’ integrity and cleanness. The automotive industry also uses stainless steel coiled pipes for fuel lines and hydraulic systems areas where performance and reliability are crucial. These varied aspects indicate the different functions and importance of stainless steel spiral pipes in contemporary industrial activities.
Usage in Fuel and Gas Systems
Thanks to their strength and resistance to corrosion, stainless steel spiral pipes have numerous benefits in a fuel and gas system. Coiled pipes are central in delivering fuel to its intended destination without interruptions, which is vital in ensuring reliability in power output and enhancing the overall efficiency of a system. In the automotive industry, stainless steel spiral pipes are now widely used for fuel lines as they are dependable in preventing leaks and high-pressure requirements. Such coiled pipes are made to withstand extremely high-temperature ranges and highly corrosive environments where these systems are usually exposed. Besides, in the case of natural gas distribution, these pipes also ensure safe passage of the gas through them as they have low odds of leaking, hence maintaining the structural operability and safety of the entire system. The combination of mechanical strength and corrosion resistance provides the ideal characteristics of the stainless coiled pipes for use in complex fuel and gas transportation systems that comply with the relevant standards.
Applications in Marine and Industrial Sectors
Due to the meager degradation rates, marine experts consider welded pipes out of seawater-resistant steel cores to be the best choice for marine applications. As for ballast tanks like structures, desalination, and transport systems on board vessels that come into contact with high saline water environments, their implementation guarantees longevity. Meanwhile, in the industrial segment, these pipes have become indispensable components within plants, processes, and systems involving controlled synthesis or processing of chemicals. Heavy-duty applications such as those encountered in industrial plants are today cost-effective because of the high structural strength required. Judging from the perspective of transparent, credible internet resources, it’s noteworthy that seamless stainless steel coiled pipes provide optimum leak-resistance design, thereby ensuring structure integrity and safety in both ocean and industrial environments.
Specialized Uses: Wort Chiller and Heating Systems
Stainless steel spiral pipes are advantageous in wort chiller and heating system applications due to their exceptional thermal conductivity and corrosion resistance. In the process of wort chilling, these pipes efficiently transfer heat, rapidly reducing the temperature of the wort post-boil to a level suitable for fermentation, which is crucial for maintaining flavor and preventing contamination. The seamless design of coiled pipes ensures minimal contamination risk, playing a pivotal role in homebrewing and commercial brewing operations.
For heating systems, stainless steel spiral pipes provide outstanding durability and reliability. They are frequently used in heat exchangers, where their ability to withstand high temperatures, often up to 600-750°F, and pressures, typically in the range of 150-300 psi, ensures consistent performance. Additionally, their corrosion-resistant nature enables them to handle water-based and chemical heating media without degradation, providing long life and reduced maintenance costs.
Technical parameters for these applications often include tube diameters ranging from ¼ inch to 1 inch and wall thicknesses from 0.049 inches to 0.083 inches, depending on the specific operational requirements. These specifications are chosen for efficiency and compliance with industry standards, reinforcing the critical role of stainless steel coiled pipes in specialized equipment applications.
How to Install and Maintain Stainless Steel Coiled Tubing?
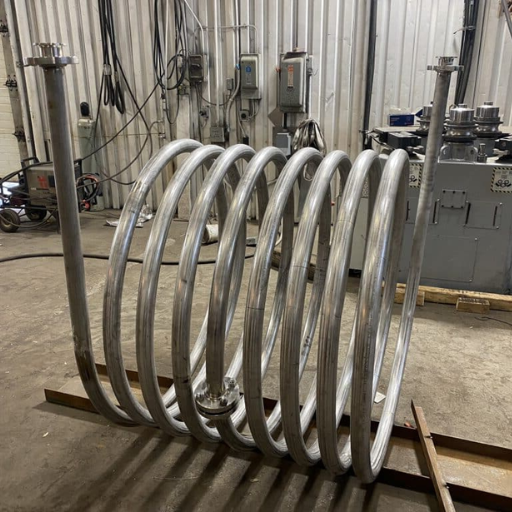
How to Install and Maintain Stainless Steel Coiled Tubing
To ensure a successful installation of stainless steel coiled tubing, it is crucial to thoroughly inspect the coiled tubing for any visible defects or damages. The tubing should be carefully uncoiled using appropriate equipment to prevent kinks or bends, which could compromise its integrity. During installation, pay special attention to securing the tubing properly with compatible fittings and connectors designed to handle the operational pressures and temperatures. Employ torque guidelines as specified by manufacturers to avoid overtightening, which can lead to leaks or damage to the tubing system.
Maintenance Guidelines:
Regular inspections and maintenance are necessary to uphold the performance and longevity of stainless steel coiled tubing. Check for signs of wear, corrosion, or fatigue in areas subject to high stress or exposure to harsh conditions. Implement a routine cleaning procedure to prevent the buildup of contaminants, mainly when the tubing is used to transport aggressive or reactive substances. Ensure all fittings and connections are tight and leak-proof, and promptly replace any worn or damaged components. By adhering to these guidelines, you can maintain the integrity of the stainless steel coiled tubing and achieve a prolonged service life in your industrial applications.
Step-by-Step Installation Guide
- Inspection: I closely inspect the stainless steel coiled tubing for any visible defects or damages. This preliminary step is crucial to ensure the tubing is free from imperfections that could compromise its integrity during operation.
- Uncoiling: I carefully uncoil the tubing using the proper equipment. This prevents kinks or bends that might affect the tubing’s efficiency and durability.
- Positioning: Next, I position the tubing according to the system layout, ensuring it’s aligned properly with any other components it will connect to. This aligns the tubing for seamless integration and functionality within the system.
- Securing: I use compatible fittings and connectors to secure the tubing in place. I select these components based on their compatibility with the system’s specified operational pressures and temperatures.
- Torque Application: I apply the appropriate torque to the fittings and connectors, following the manufacturer’s guidelines. This prevents overtightening, which can lead to leaks or system damage.
- Final Inspection: I conduct a thorough final inspection to ensure all connections are secure and leak-proof before commencing system operations. This step confirms the integrity and readiness of the installation for immediate use.
Maintenance Tips for Longevity and Corrosion Resistance
I follow a more proactive approach to maintaining stainless steel coiled tubing based on the practices of leading companies in the industry. Foremost, I inspect the tubing more frequently and look for stress corrosion or wear, especially in areas with the most significant stresses and risk factors. Tubing systems must be cleaned occasionally to remove contaminants, mainly when aggressive or corrosive substances are present. Under normal circumstances, all the fittings and connections are checked, and their tightening is performed to prevent leakages. Compromised components are routinely replaced to ensure intactness of the interconnecting components and the system as a whole.
In the case of the technical parameters, I check to ensure that the temperature and pressure of the tubing in operation do not go beyond the recommended limitations, which generally are 750°F and 300 psi, respectively, for heat exchangers. Likewise, ¼ inch to 1-inch diameters and wall thicknesses of 0.049 inches to 0.083 inches are checked to confirm that the tubing’s integral dimensions conform to the application’s requirements. Such practices as care exist and are essential in enhancing the performance and efficiency of the stainless steel coiled tubing.
Common Issues and Troubleshooting
Leaking is frequently associated with one reason or another, and the most common of all reasons would probably have to be the leaking of the stainless steel coiled tubing, which is a common problem. Although it has general resistance, it may rust over a period due to certain elements’ exposure or some extreme environmental effects. In this regard, the tubing is cleaned as per industry standards every few days, and additional protective coatings are also suitable to prevent the tubing from wearing away.
Another common concern is leakage, which can be attributed to faulty installation or fittings that are past their service life. When I identify visible leaks, all the connections and other fittings are fans. How iwysghtl for thoroughness and damage due to strain and fatigue with replacement where necessary? Th Paulvra’s problem can be resolved by using a precise torque range during installation.
Particulate-laden media should also be avoided since they can be a major cause of clogging when passing through industrial tubing systems. To do this, I establish a standard operating procedure for cleaning and make sure that all filters and strainers are functioning properly to prevent debris from entering the tubing.
Last but not least, cycles of stress and deformation are often encountered at high-pressure applications, and fatigue in such cases often leads to the cracking up of the tubing. This is dealt with by routinely spying for the tiniest of cracks in high-stress areas, and any tubes that are damaged in such areas are removed as soon as possible. These troubleshooting measures enable me to to meet the desired operating conditions and safety of the tubing system.
Frequently Asked Questions (FAQ)
Q: What is the main advantage of using a stainless steel spiral pipe?
A: Stainless steel coiled pipe offers versatility and durability, making it suitable for a wide range of applications, such as plumbing, automotive, and marine. It is known for its resistance to corrosion and high working pressure, making it an ideal choice for commercial and DIY projects.
Q: How does 304 stainless steel compare to 316 ss in coiled pipes?
A: 304 stainless steel is a commonly used grade with good corrosion resistance and affordability. In comparison, 316 ss, also known as marine-grade stainless steel, provides superior corrosion resistance and is ideal for marine applications. Both grades are available in spiral pipes and can meet different project requirements.
Q: Can stainless steel coiled pipes be used for brake lines?
A: Yes, stainless steel spiral pipes are suitable as stainless steel brake lines. They provide high resistance to corrosion and mechanical stress, ensuring reliable performance and safety in automotive applications.
Q: What sizes and lengths do stainless steel coiled pipes come in?
A: Stainless steel coiled pipes are available in a variety of sizes and lengths, such as 50-ft and 100-ft coils. They are also offered in different OD (outer diameter) measurements to meet various specifications and project needs.
Q: Are seamless and welded options available for stainless steel coiled pipes?
A: Yes, stainless steel spiral pipes are available in seamless and welded options. Stocking both options ensures you can choose the type that best suits your application, whether it requires enhanced strength or specific welding characteristics.
Q: What should I know about the working pressure of stainless steel coiled pipes?
A: The working pressure of stainless steel coiled pipes varies depending on the grade and size. They are designed to withstand high psi levels and meet ASTM standards, making them suitable for high-pressure applications.
Q: Are stainless steel coiled pipes suitable for portable and DIY projects?
A: Yes, stainless steel spiral pipes are ideal for portable and DIY projects due to their malleability and ease of handling. They are lightweight and can be used in applications such as camping gear, portable showers, etc.
Q: How are stainless steel coiled pipes shipped?
A: Stainless steel spiral pipes are typically shipped in coils, which makes them easy to transport and handle. This packaging method helps maintain their integrity and prevent damage during transit.
Q: Can stainless steel coiled pipes be used in beverage and bath applications?
A: Yes, stainless steel spiral pipes are perfect for beverage and bath applications due to their premium quality and resistance to contamination. They ensure clean and safe fluid handling in environments where hygiene is a priority.
Q: Where can I find more information about specific stainless steel spiral pipe products?
A: Detailed information about specific stainless steel coiled pipe products, including specifications and availability, can typically be found on the supplier’s product page. It is advisable to check these resources to ensure you select the suitable pipe for your needs.